Starch ether
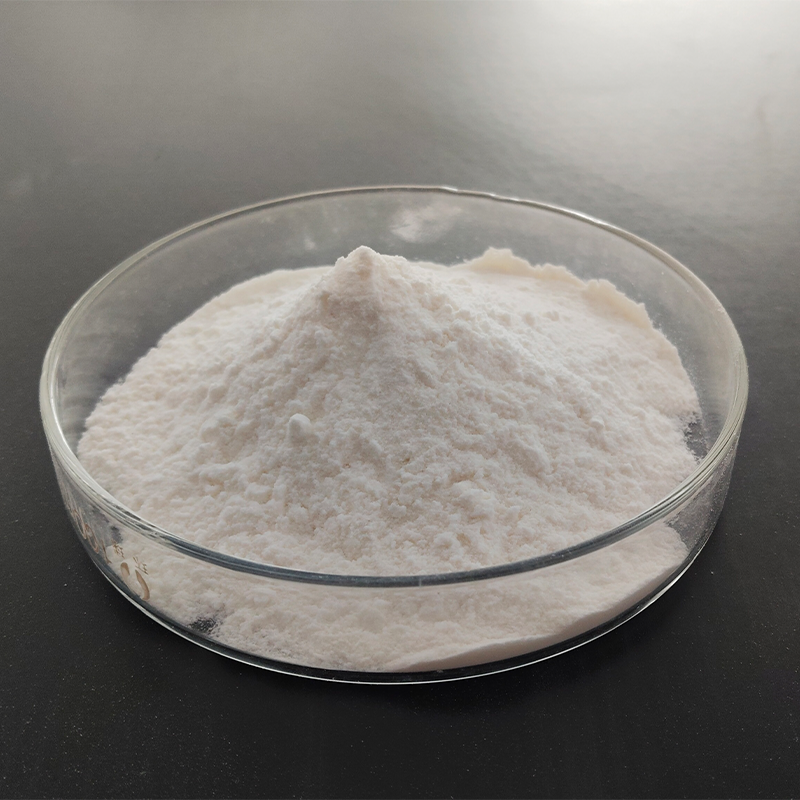
Starch Ether Product Introduction
1. Product Description
Starch Ether is a water-soluble polymer derived from natural starch (corn, cassava, potato, etc.) through etherification reactions (introducing carboxymethyl, hydroxypropyl, or cationic groups). Its molecular structure combines the eco-friendliness of natural starch with the tunable functionality of synthetic polymers, making it widely applicable in construction, food, pharmaceuticals, and other industries.
Classification:
Carboxymethyl Starch Ether (CMS): High water solubility, suitable for neutral to alkaline environments.
Hydroxypropyl Starch Ether (HPS): Excellent salt resistance and high-temperature stability.
Cationic Starch Ether: Positively charged, designed for adsorption in negatively charged systems (e.g., wastewater treatment).
Physical Form:
Powder: White to off-white, free-flowing, adjustable particle size (80–200 mesh).
Granules: Pre-gelatinized type for rapid dissolution.
Solubility:
Disperses in cold water and forms a transparent viscous solution when heated to 50–80°C (viscosity: 100–10,000 mPa·s).
2. Specifications
Parameter | Typical Value | Test Standard |
---|---|---|
Degree of Substitution (DS) | 0.2–1.5 (customizable) | GB/T 12033-2008 |
Viscosity (1% solution) | 100–10,000 mPa·s (25°C) | Brookfield RV/HA Viscometer |
pH (5% solution) | 6.0–8.0 | GB/T 9724-2007 |
Moisture Content | ≤10% | GB/T 12087-2008 |
Ash Content | ≤5% | GB/T 22427.5-2008 |
Particle Size | 80–200 mesh (customizable) | Laser Particle Size Analyzer |
Heavy Metals (Pb) | ≤5 mg/kg (food grade) | GB 31644-2018 |
3. Key Characteristics
Thickening & Rheology Control:
Shear-thinning behavior (pseudoplastic fluid), ensuring anti-sagging properties at rest and smooth flow during application.
Viscosity linearly adjustable via concentration and temperature (suitable for spraying or troweling).
Chemical Stability:
Resistant to pH 3–12, salt (NaCl ≤10%), and high temperatures (up to 100°C for select grades).
Water Retention & Film Formation:
Extends open time (≥30 minutes) in construction materials by preventing rapid water evaporation.
Forms flexible transparent films to enhance surface strength in paper or textiles.
Eco-Friendliness:
Biodegradation rate ≥90% (28 days, OECD 301B standard), zero VOC emissions.
4. Product Advantages
Aspect | Advantages |
---|---|
Cost Efficiency | 20–30% lower cost than cellulose ethers (e.g., HPMC), offering superior ROI. |
Tunable Performance | Customizable viscosity, dissolution speed, and thermal stability via DS and molecular weight adjustments. |
Compatibility | Synergizes with cement, latex powder, and inorganic fillers without interfering with other additives. |
Certifications | Complies with FDA 21 CFR 172.892 (food grade), REACH (EU), and GB 31644-2018 (China). |
5. Application Fields
Industry | Typical Applications | Recommended Grades |
---|---|---|
Construction | - Putty powder/tile adhesive: Anti-sagging, easy application - Mortar: Water retention, crack reduction | CMS-0.6, HPS-0.8 |
Food Industry | - Ice cream/yogurt: Stabilizer (gelatin replacement) - Sauces: Thickening, anti-separation | CMS-F (food grade) |
Pharmaceuticals | - Tablets: Binder (PVP alternative) - Sustained-release capsules: Drug carrier | HPS-M (medical grade) |
Textile & Dyeing | - Printing paste: High-definition patterns, easy wash-off - Warp sizing: Cost-effective PVA replacement | CMS-T (textile grade) |
Paper Industry | - Surface sizing: Water resistance enhancement - Coating additives: Improved printability | HPS-P (paper grade) |
Personal Care | - Shampoos: Thickening, particle suspension - Face masks: Film-forming, moisturizing | CMS-C (cosmetic grade) |
6. Production Technology
Process Flow:
Raw Material Pretreatment:
Starch slurry gelatinization (60–80°C) to disrupt crystalline structures.
Etherification Reaction:
CMS: Starch + chloroacetic acid → NaOH catalysis, 50–60°C for 4–6 hours.
HPS: Starch + propylene oxide → Alkali catalysis, pressurized reactor at 60–80°C.
Post-Treatment:
Neutralization (HCl to pH 6–7), centrifugal washing, spray drying (inlet air: 180–200°C).
Key Equipment:
Reactors (with agitation and temperature control), centrifuges, spray dryers, milling/sieving machines.
Quality Control:
DS Measurement: Titration or NMR.
Viscosity Stability: Accelerated aging test (40°C/75% RH, 30 days).
7. Theoretical Mechanism (Theory)
Etherification Chemistry:
Hydroxyl groups (—OH) at C2/C6 positions of starch molecules are replaced by ether groups (—O—CH₂COOH or —O—CH₂CHOHCH₃), disrupting hydrogen bonding and enhancing hydrophilicity/flexibility.
DS vs. Performance:
Low DS (0.2–0.5): Poor cold-water dispersibility, requires heating for dissolution, superior film-forming.
High DS (>1.0): Rapid cold-water solubility, high viscosity, but increased film brittleness.
Rheological Behavior:
Molecular chain entanglement forms a 3D network, exhibiting shear-thinning (thixotropy), ideal for high-shear applications like spraying.
8. Services & Support
Customization: Adjust DS, particle size, dissolution speed (e.g., instant or slow-dissolving types).
Technical Consulting: Formulation optimization (e.g., HPMC blending ratios of 1:1–1:3 in tile adhesives).
Testing Services: Third-party reports (SGS, Intertek) for viscosity, heavy metals, and microbial limits.
Logistics: Standard 25 kg/bag packaging or bulk ton bags, global shipping to major ports.
9. Packaging & Storage
Item | Description |
---|---|
Packaging | - 20–25 kg/bag: Inner moisture-proof aluminum foil + outer PP woven bag - Ton bags (500–1000 kg) |
Storage Conditions | - Temperature: <30°C - Humidity: <60% RH - Avoid contact with oxidizers/strong acids |
Shelf Life | 24 months unopened; use within 6 months after opening (reseal to prevent moisture). |
10. Safety & Precautions
Operational Safety:
Dust Control: Wear N95 masks to avoid respiratory irritation from prolonged inhalation.
Eye Contact: Flush immediately with water for 15 minutes; seek medical attention if necessary.
Environmental Handling:
Waste Disposal: Treat as general industrial solid waste (incineration/landfill per local regulations).
Effluent Treatment: Neutralize to pH 6–8 before discharge.
Food-Grade Use:
Use only CMS-F/HPS-F grades; strictly separate from industrial-grade products in storage.
Conclusion
Starch ether, with its renewable origins, customizable performance, and eco-friendly advantages, is rapidly replacing traditional synthetic polymers (e.g., HPMC, PVA) as a representative of green chemical materials. For samples, technical data, or custom solutions, contact our technical support team!
Note: Data based on typical industrial-grade products. Actual parameters subject to test reports or technical agreements.